- Amanda
- October 5, 2016
Why aren’t all belt conveyor solutions are the same
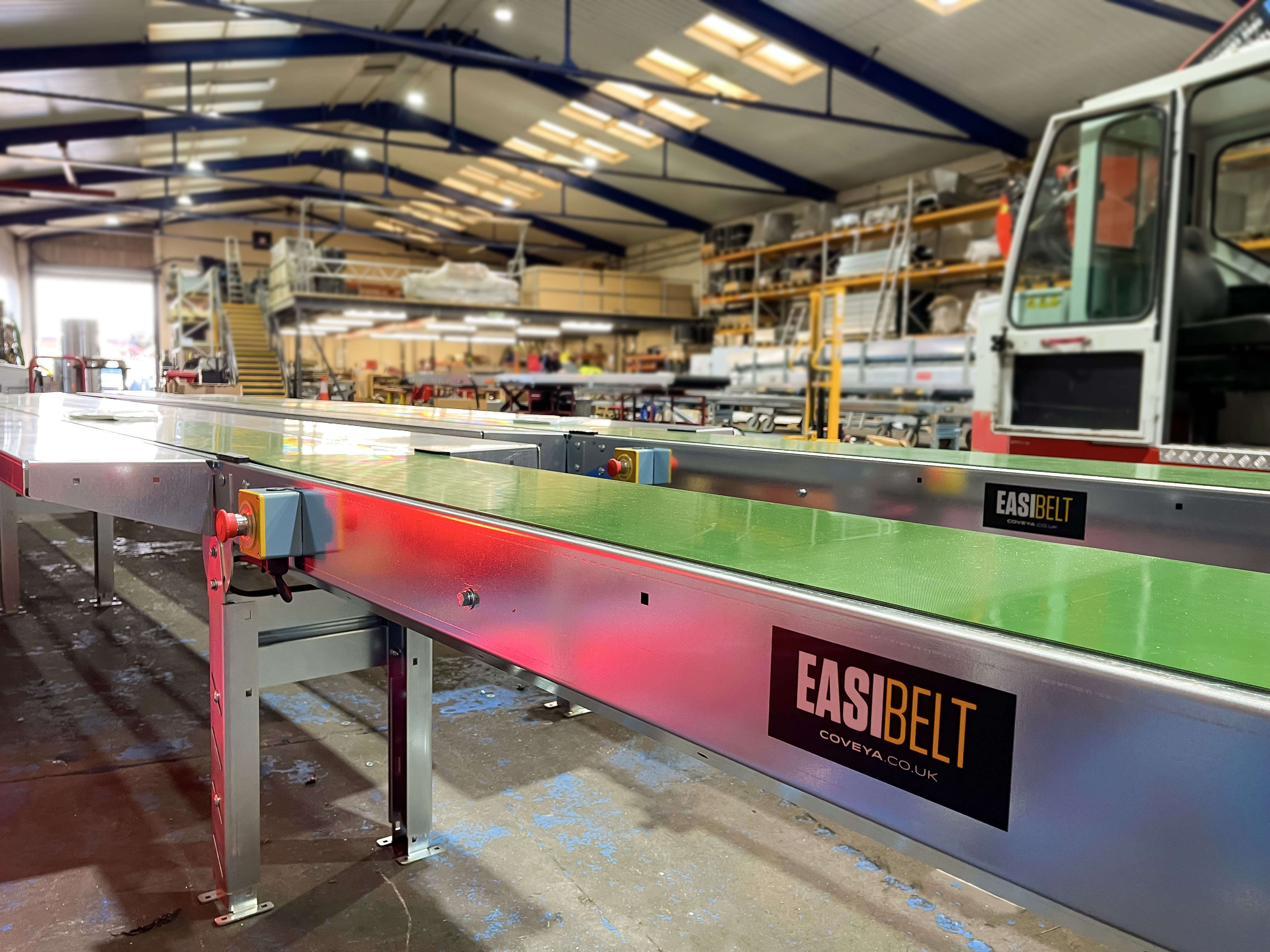
As you would expect, not all belt conveyor solutions are the same. The necessity of having a conveyor system that can operate in tough environments almost goes without saying – but making the correct choice might be a daunting prospect.
The risk of downtime through breakdowns, is something every operator wants to avoid at all costs. First and foremost consideration should be that whoever supplies your conveyor, must be able to provide support and a fast response that keeps you up and running.
Whoever supplies your conveyor must be able to provide support, fast!
At the outset, it’s important to obtain a site survey which should be provided free of charge by your supplier. A site survey carried out by a specialist, experienced in material handling in tough environments, will be able to help you achieve the best solution for your particular application. This is an important part of the process that shouldn’t be underestimated. Expert advice can help you avoid problems such as the use of numerous small or under-powered conveyors on a project (with inherent labour and reliability problems), when perhaps one bespoke conveyor, properly designed and implemented could solve your problem much more efficiently.

Your supplier should also be able to provide you with relevant drawings to help get appropriate approvals and licenses.
Making the right choice
Once the conveyor design and ergonomics have been decided, the next thing is to sort out the technicalities of the equipment.
This includes decisions on usage, throughput and speed requirements, along with belt type, widths and relevant accessories.
The right decisions made at this stage can also add to overall efficiency.
For example, many conveyor systems are restricted to 15mm chevron patterns on their belts, which not only limits their carrying capacity, but also efficiency when it comes to working on inclines. The higher the chevron pattern, the higher the incline that is achievable with the conveyor. It is possible to incorporate belts with a 50mm cleat on the belt or even with ‘scoops’ or ‘lips’ to enhance capacity and performance when working at angles.
These considerations may sound daunting, and it is possible that going through this sort of process is what makes some site or project managers hesitant about utilising such technology, preferring to stick with how they’ve done things before and what they know. But your supplier will be able to take the problem out of your hands, right through to installation, maintenance and dismantling at the end of a project.
The onsite benefits
Conveyor systems can help provide efficiencies on sites with restricted access, where considerable excavation and demolition work is required, and where materials need to be transported from one place to another.
In these instances, if you select the correct conveyor system for your application, you may find it can offer a much faster solution than other generally utilised methods (i.e. wheeled plant etc). It is possible, in some cases, to shift in up to 500 tons of materials per hour with a single conveyor, creating huge savings in manpower and machinery which in turn will have a knock-on effect on the time it takes to complete other related tasks – i.e. minimising downtime and waiting around.

The long-term benefits from making the correct conveyor choice at the outset are huge! Don’t risk getting it wrong!
Get in touch
Why not let Coveya see how much time and money you could save?