- Amanda
- October 11, 2016
Belt joints: Mechanical vs vulcanised
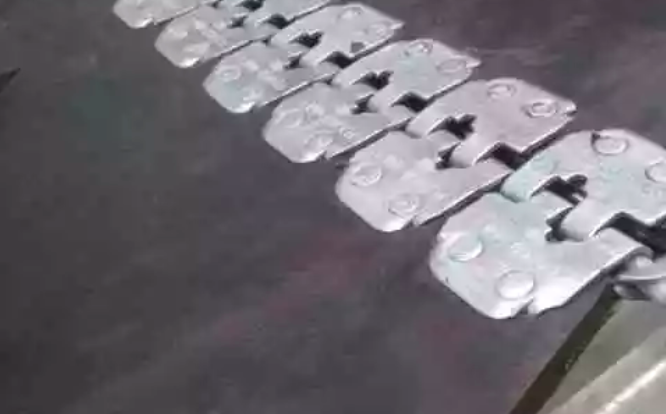
A critical area of importance on any conveyor system is the belt joint, and in most applications, there are two preferred types of splicing methods: mechanical splicing, which joins belt ends by metal hinges or plates; and vulcanised splicing, which joins belt ends through heat and/or chemicals.
Understanding the pros and cons of each splicing method is important when making a decision on which splicing method to use. What are the environmental factors that might affect the splice? Are workers up against time constraints? What are the costs associated with long conveyor downtimes? These are just some of the questions to ask when choosing between mechanical fastening and vulcanisation.
The vulcanisation process
Vulcanisation is an involved procedure that can offer a smooth splice with minimal risk of snagging, tearing and other harmful wear to the belt. There are two types of vulcanising processes, hot and cold. Each process requires unique tools and an intimate knowledge of the rubber bonding process.
Hot vulcanisation splices are heated and cured under pressure with a vulcanising press. Cold vulcanisation does not use a press, but uses a bonding agent that causes a chemical reaction to splice the two belt ends together.
The entire process for the vulcanising of a belt takes several hours depending on working conditions. Because vulcanisation often requires time for a specialised crew and equipment to be brought onsite, operations can be shut down for prolonged periods and ultimately, may cost hundreds of pounds per splice, considering material and labour – and that is before considering the cost of downtime.

Vulcanising of a belt takes several hours!
Mechanical splicing
There are several types of mechanical fasteners, each created for use with different belt widths, lengths, thicknesses, speeds, tensions and cleaners.
No matter what the belt condition, mechanical fasteners are a good choice for both new and older, worn belts. These fasteners can easily be separated by removing the hinge pin and are essential in applications where belts need to be frequently be removed, extended or shortened. The hinged fastening system permits separate halves of the belt to be pre-spliced, requiring only the hinge pin to be inserted on site.
Mechanical fasteners are installed quickly and easily, onsite. The mechanical splice installation tools are easily transported to the job site and offer versatility in installation methods. These splices can be installed with as little as a basic installation tool and hammer, or with a modified installation tool and choice of electric or air power source

Mechanical fasteners are installed quickly and easily
Every splicing method has its limitations and it is essential to understand what these are:
- The speed and simplicity of mechanical jointing represents major advantages over vulcanisation
- Mechanical splicing offers reduced belt waste (vulcanising uses extra belt length)
- Type of material being handled may affect certain types of joint. i.e. dried sewage cake contains chemicals that can corrode steel mechanical clip joints
- Vulcanised joints have the highest practical strength
- A vulcanised joint will prevent any leakage and material sift-through as the joint is continuous
- Mechanical fasteners generally are noisier than vulcanised joints
- Old and/or worn fabric belts are not well-suited to vulcanisation
- You can’t vulcanise anytime, anywhere – you need clean, dry and relatively warm conditions
- Because a mechanical splice is visible, wear and deterioration is visibly apparent and can be taken care of before a complete belt failure. Vulcanised splices, in contrast, typically deteriorate from the inside out due to poor adhesion and signs of wear may come too late for any preventive measure
- Longevity – a vulcanised belt joint will nearly always outlive a mechanical splice
Conclusion
When a splice needs to be made, decide which method will work better based on environmental and working conditions around the belt. Temperature, moisture levels, residue, the material being carried and amount of belt slack you have can all come into play. Both splicing methods can be reliable options, but one may work better over the other in certain scenarios.
Get in touch
Why not let Coveya see how much time and money you could save?