- Amanda
- November 24, 2020
What Types of Conveyor Belts Are There?
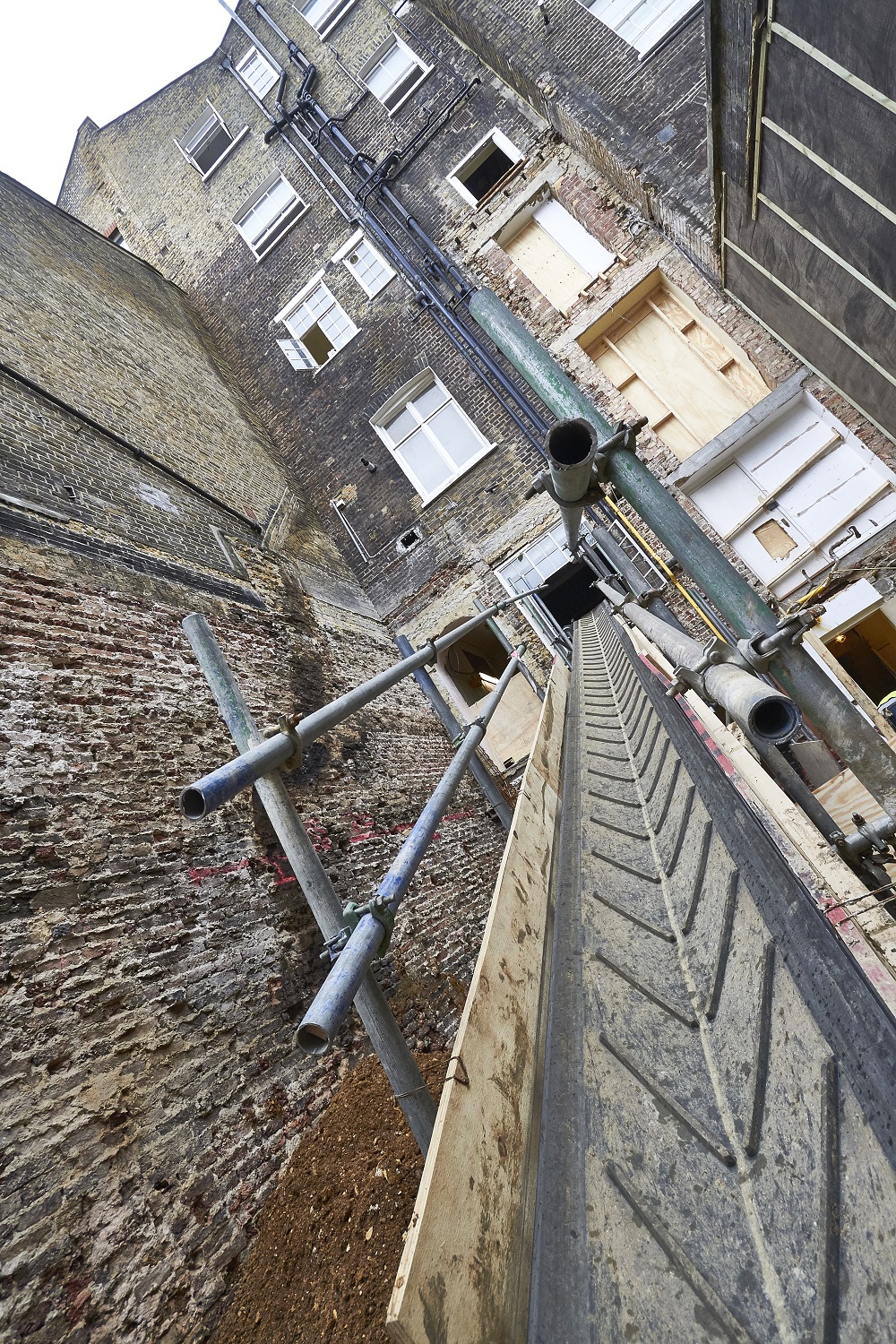
For over 30 year’s Coveya has supplied a wide range of conveyors to support many different industries and applications. Our conveyors come in a variety of widths and lengths and with a commitment for innovation, design, and quality conveyor solutions, we can supply or design a bespoke conveyor for you.
Conveyor belts play an important part in efficiently moving materials but what are the three main types of conveyor belt?
Plain Belt – It has a plain smooth rubber surface which is perfect for moving materials horizontally or at very shallow inclines, however, it can also be used at steeper inclines when sticky and cohesive materials are used. The main benefit of a plain belt conveyor is that it can easily be scraped clean using a scraper, so the conveyor doesn’t get clogged up.
Chevron Belt – Chevron belts are often used for “loose” material such as granular aggregates or demolition rubble at medium inclines. Chevron belts can be cleaned via a “finger” scraper.
Flighted Belt – 50m flighted belts are used for much steeper inclines and can work at 45° depending on the speed of the conveyor and the types of material being moved. Flighted belts offer the best material movement solution for loose aggregates, excavation spoils or even large items like bricks, blocks or bagged materials.
Coveya is one of the largest and most respected supplier of Conveyors in the UK and we can help you find the right conveyor for your project. For more information call us on 0117 956 3131