- Amanda
- May 23, 2017
Why health and safety is vital for your bottom line
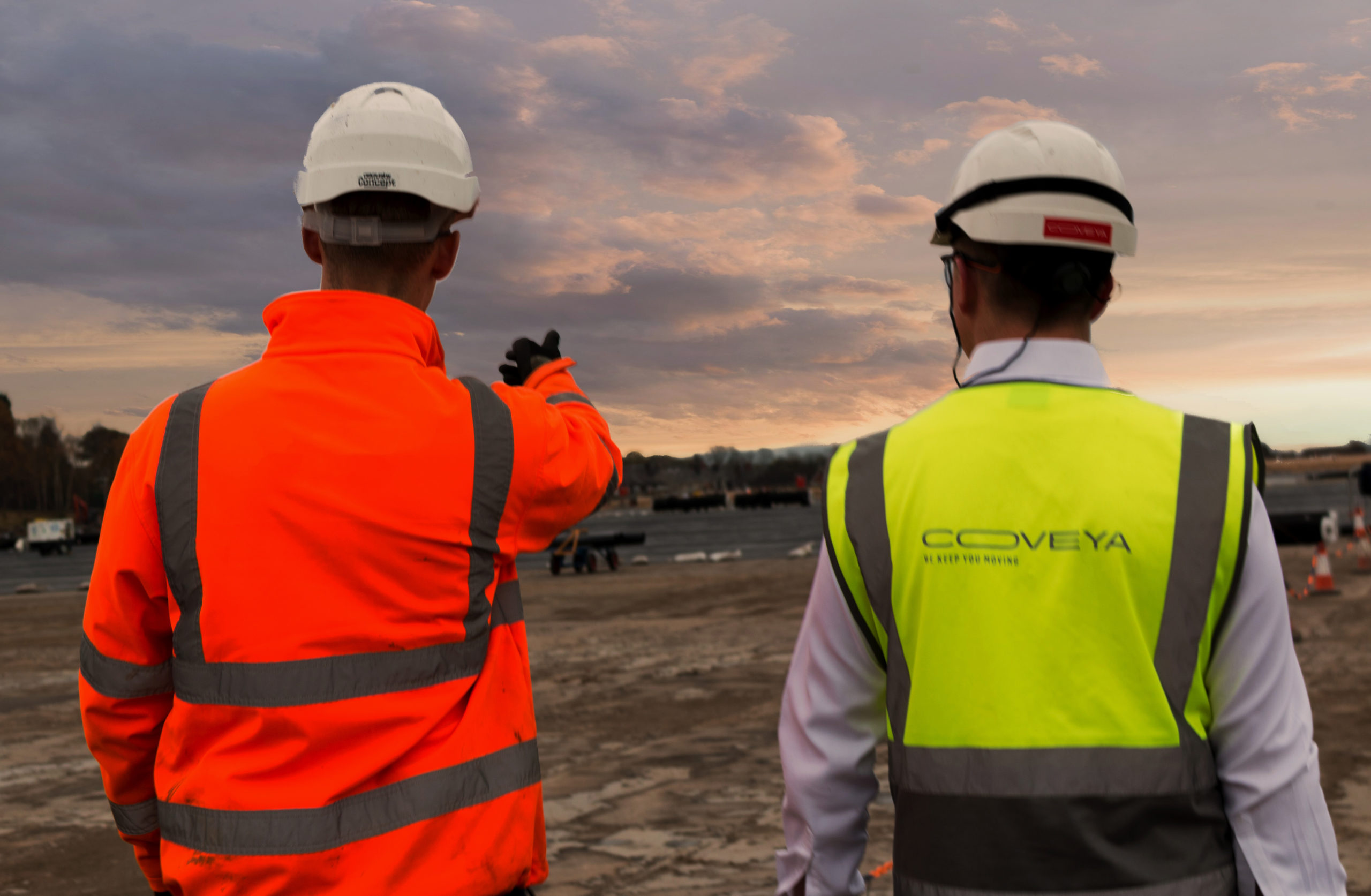
Are your wage costs doubling? A single health and safety incident can cause your wage costs to skyrocket. Here’s how to keep your budget in check…
In the UK alone, from 2015 to 2016, 30.4 million working days were lost due to work-related accidents or illnesses, with 44,000 workplace injuries and nine fatalities caused by moving machinery.
Just think of the implications of this. Not only must a company pay the salary of absent employees, but they must also fork out for overtime to cover lost hours. Then add to this, lost output and productivity and the time needed to train someone else to fulfil the absent employee’s role. Quite an impact!
Read our case study in which Coveya was able to help significantly reduce the risk of injury for the construction team.
Health and safety starts with you!
We all know that health and safety regulations are a legal responsibility for any company. However, rather than viewing it as a chore, it’s essential to see health and safety as an integral and beneficial part of your business or site management. Consider some of the benefits of effective health and safety management. You will:
- Protect your workers and prevent unnecessary problems and suffering
- Reduce absences and the costs that go with them
- Improve productivity and, in turn, profits
- Maintain a great reputation as a safety-conscious employer
- Retain valued, hard-working team members
- Reduce legal costs and time spent dealing with work-related injury cases
Although the types of workplace injuries that occur each year are similar in nature, the good news is, the average number of yearly injuries is in decline. So, what can you do to ensure effective health and safety management while using conveyors on your site?
Engineer’s tip: The conveyor likes to be loaded little and often.
Key safety points for conveyor belt usage
Here are four tips from our in-depth conveyor health and safety guide. To see all ten tips, check out How to Use a Conveyor Safely: Ten Things Every Operative Should Know
1. Know the nip points and ensure guards are fitted at all times.
A nip point is a hazardous area of a conveyor belt, in which moving parts meet, creating the potential for severe injury when items such as tools, hair, fingers or limbs get caught between them. To prevent such accidents and injuries, you should be aware of where the nip points are located on your conveyor belt and ensure that hazardous areas are always fitted with a guard.
2. Wear Personal Protective Equipment (PPE) suitable for the task and work area.
Whether it’s a hard hat, safety shoes, gloves or ear defenders, appropriate PPE is a vital part of health and safety on your building site. Tucking away hair and loose jewellery that could get caught in the conveyor belt is also essential.
3. Be aware of your surroundings and be alert for any potential hazards.
Health and safety is everyone’s responsibility. Maintaining focus, keeping your eyes open for potential hazards and taking prompt action can prevent serious incidents.
4. Schedule and carry out regular maintenance checks.
A systematic approach to regular maintenance inspections can keep your conveyor belt working properly and identify any issues before they cause injury. Your operation manual contains a checklist for the daily and weekly checks that must be carried out.Top tip: Watch out for nip points, where moving parts of a conveyor meet.
Nip points create the potential for serious injury when clothing, fingers, hair or tools get caught in the machine. Check out our infographic, Conveyor Belt Hazards: Know Your Nip Points for a quick visual guide.
‘Plan, Do, Check, Act’ (PDCA) approach
In recent years, HSE has actively promoted the ‘Plan, Do, Check, Act’ approach for workplace health and safety. The PDCA is a four-step management method used by businesses to continually improve and fine-tune services, products and processes. Each stage overlaps with the next.
Rather than viewing health and safety as a one-off process or a standalone system, the PDCA approach is designed to be an automatic procedure that is repeated each time a change is made, helping companies to see it as an integral part of their ongoing business management.
So, how can you use the PDCA approach when it comes to using a conveyor belt on site?
Plan
Writing a health and safety policy, specific to your site and conveyor belt is an excellent place to start. Set out your aims and objectives and how you will achieve them, and decide on key roles and responsibilities within your team. Identifying possible risks and safety hazards and outlining how you will comply with regulations is key to this step. Additionally, you will need to decide how to measure results and set up any relevant training your staff need to use the conveyor belt safely.
Do
So, you’ve made a plan, now you need to execute it. This stage involves an in-depth risk assessment around your conveyor belt to identify potential hazards. Action should then be taken to put practical risk control measures into place. Organisation and efficient communication are vital to implementing your plan, as is providing the appropriate resources, equipment and training your staff need to complete the job safely.
Check
Effective health and safety involves more than detailed paperwork; you need to make sure your original plan is being carried out consistently. Measure your results and supervise onsite conveyor procedures to ensure your plan achieves your aims and controls risks. If there have been any accidents or near misses, now is a good time to investigate these further.
Act
The PDCA is an ongoing process. When it comes to the effective and safe use of conveyor belts, taking action on lessons learned is vital. At this stage, you should review your performance and learn from any incidents or near misses. Change your policy and/or plan going forward to prevent issues or accidents from occurring again.
Often, you’ll find that even small tweaks to your health and safety policy can yield rich results, with the benefits to you and your workers far outweighing the time you invest in effective health and safety procedures.
Find out more
For further information on keeping operatives safe and minimising the risks associated with working with conveyors, take a look at the Coveya Knowledge Base or visit the Health and Safety Executive (HSE) website.
Coveya can offer a wide range of conveyors to suit every project. Why not let Coveya see how much time and money you could save?